往复压缩机无级气量调节系统
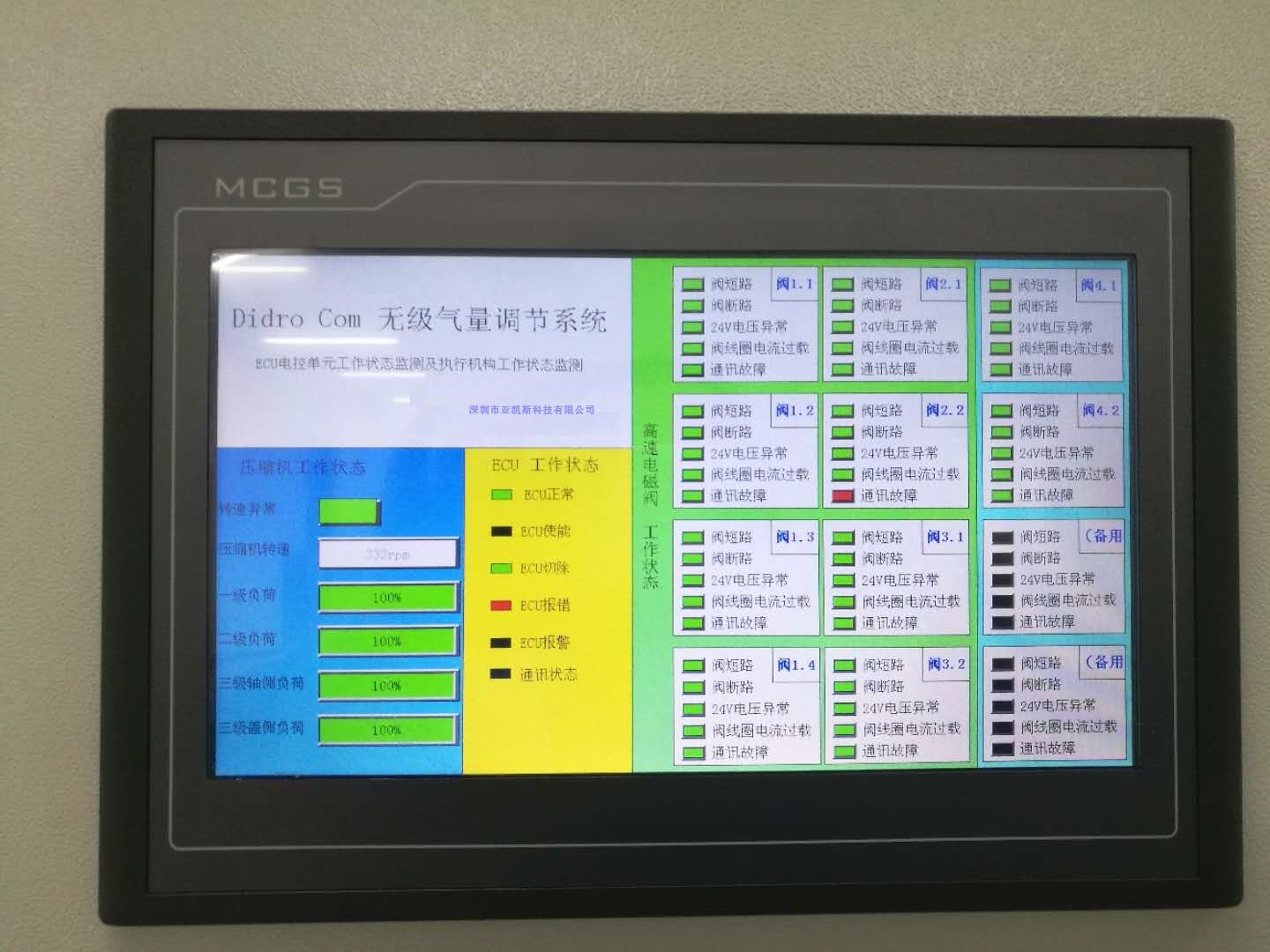
往复压缩机无级气量调节系统
1、往复压缩机的工作原理及特点
往复式压缩机有四个工作过程:压缩(A-B)、排气(B-C)、膨胀(C-D)、吸气(D-A),见图1所示,四条线所包围而成的面积就是压缩气体所消耗的功。排气时的气缸压力要高于排气管道的压力,高出部分的压力用于克服气阀弹簧力、阀片的惯性、流动阻力,这就是“排气阀损”,见图1的BCB″的面积。排气结束后,余隙容积的气体是无法排出的,是要进行膨胀的。余隙容积包括:活塞端面与气缸端面之间的止点间隙的容积、气阀至气缸容积的通道所形成的容积、气缸镜面与活塞外圆之间的间隙容积。吸气时的气缸压力要低于吸气管道的压力,低出部分的压力用于克服气阀弹簧力、阀片的惯性、流动阻力,这就是“吸气阀损”,见图1的ADD′的面积。
炼油装置往复式压缩机的额定流量,一般都是根据装置所需的最大流量或近期装置可能扩容所需的流量来确定的。但是,由于入口条件的改变(如介质组分、入口压力、温度等)、工艺流程或耗气设备的需求量改变,压缩机负荷都会发生变化。当耗气量小于压缩机的排气量时,为了使压缩机的排气量适应耗气量的需求,保持管网中的压力稳定,就需要对压缩机进行气量调节,并要求灵活控制。
图1 往复式压缩机工作过程
2、无级气量调节系统的工作原理及特点
2.1传统气量调节方式
传统气量调节方式及其特点如下:
1)旁通回流调节
排气管经由旁通管路和旁通阀门与进气管相连接,调节时只要开启旁通阀,将过量的压缩气体通过中冷器和控制阀,从压缩机的排气侧导入吸气侧。
特点:可实现无级自动调节,调节范围大并可靠,调节灵活;多余气体全部压缩,在所有的调节法中,旁路法能耗最高,运行经济性差;一般都是与其他调节方法共同使用,适用于调节幅度小的场合。
2)余隙腔调节
在压缩机的气缸上,除固定余隙容积外,另外设有一定的空腔,调节时接入气缸工作腔,使余隙容积增大,容积系数减小,排气量降低,实现气量调节。特点:需要较多的人工干涉,系统可靠性较动设备差;调节响应速度较缓慢;易损件多,难于维护,不适用于已有设备改造。
3)转速调节(变频器)
通过改变压缩机的转速来改变单位时间内压缩气缸的压缩次数从而达到调节排气量的目的。
特点:用于驱动机为内燃机或汽轮机的压缩机或驱动电机功率较小的压缩机;低转速时,对压缩机工作产生不良影响,如气阀颤动、润滑不充分等;对于大功率电机驱动的压缩机,变频器成本较高;调节气量连续,功率消耗小;压缩机各级压力比可保持不变,压缩机上不需设专门的调节机构。
4)卸荷调节法
该调节方法是在气缸的进气阀上安装卸荷器,在吸气及压缩过程中,它使气阀密封元件处于开启位置。吸气时,气体从压开的吸气阀吸入气缸,压缩过程中,气体又从压开的吸气阀重新回到吸气管线中。卸荷器处于卸荷状态时无法形成有效的压缩功,对压缩机进行流量调节。对双作用气缸,可实现0%、50%、100%的流量调节。
2.2无级气量调节系统
压缩机的能耗主要与每次循环过程中实际压缩的气量成比例。气量无级调节技术结合智能控制技术,通过液压传动装置使压缩机在压缩过程中,进气阀成为受控气阀,即通过延迟关闭进气阀的方式,使气缸中的部分气体返回进气腔,从而实现在部分行程压开进气阀的气量调节方式。如图1所示,在压缩机的活塞往复运动中,当气缸进气终了时,进气阀的阀片在执行机构作用下仍被卸荷器强制地保持开启状态,压缩过程并不沿原压缩曲线由位置A 到位置B,而是先由位置A到达位置A′,此时原吸入气缸中的部分气体经被顶开的进气阀回流到进气管而不被压缩;待活塞运动到特定的位置A′(对应所要求的气量)时,执行机构使顶开进气阀片的强制外力消失,进气阀片回落到阀座上而关闭,气缸内剩余的气体开始被压缩。这就是“回流省功”的原理。
3、无级气量调节系统组成
无级气量调节系统采用模块化设计,方便应用到已使用和新的压缩机。流程控制在DCS系统或闭环控制器上完成;CIU承担执行设备与DCS交换数据。
图2 结构组成图
图3 实物图
4、应用情况及前景
该系统在国内只有少数高校在进行研究,还未有相关企业介入,目前市场上常见的无级气量调节系统主要是德国贺尔碧格公司的产品,但其价格昂贵,供货周期长。因此,该系统可实现大型往复式压缩机的高精度气量调节,大大降低能耗,节约能源和成本,在一定程度上填补了国内相关产品空白,具有的较大技术创新性。
无级气量调节系统通过进气阀的延迟关闭,使多余部分气体未经压缩而重新返回到进气总管,节省了压缩机外回流所做的无用功,获得了显著的节能效果。从实际应用来看,投用无级气量调节系统后,在装置满负荷工况下,压缩机50%的负荷即可满足工艺系统的要求。如某加氢裂化装置,压缩机主电机的电流较之以前减少100A。主电机的电压为6000V,若电机功率因数按0.8,每度电价按0.68元,一年运行按8400h计算,一年可节省电费475万元。无级气量调节系统投用后,即维持了压缩机自身的自动控制逻辑不变,又优化了气量控制方案,使压缩机的整个控制功能更趋合理,操作更简单方便,可以实现压缩机的平稳加载、无冲击切换及停机,改善了机组的运行状况。同时,降低了开机时对工艺系统的影响,系统工艺参数更加稳定,压缩机的运行更加平稳。